In a custruzzione muderna di l'ingegneria, u dragamentu hè un ligame indispensabile, in particulare in i campi di l'ingegneria civile è di a gestione ambientale. Cum'è strumentu di trasportu flessibile,tubu flottanteghjoca un rolu impurtante in i prughjetti di dragaggio per via di a so facilità d'installazione èmobilità.
Principiu di funziunamentu di u tubu flottante per u trasportu di materiale
Durante l'operazioni di dragaggio, i tubi flottanti cunnettanu a nave di dragaggio à u puntu induve u fangu hè scaricatu (cum'è una stazione di movimentazione di materiali à terra o una nave di trasportu). U tubu flottante pò adattà a so pusizione cù u muvimentu di u flussu d'acqua o di e navi, riducendu l'impattu nantu à e navi è l'attrezzatura operativa è mantenendu a continuità di u trasportu di materiale. U tubu flottante CDSR pò adattassi à diversi ambienti acquatici è cundizioni operative.
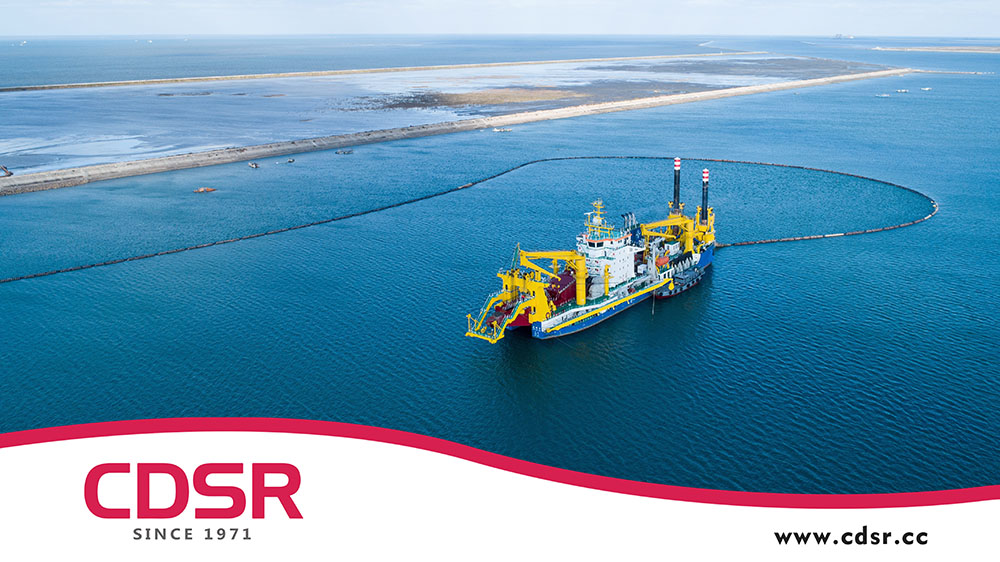
Velocità critica
A velocità critica hè a velocità ottima chì pò assicurà chì e particelle solide ùn si sedimentinu micca è evità una perdita eccessiva d'energia quandu u materiale scorri in a pipeline. Quandu a velocità di u fluidu hè più bassa di a velocità critica, e particelle solide in u fangu si sedimenteranu, causendu un bloccu di a pipeline. Quandu a velocità di u fluidu hè più alta di a velocità critica, l'usura di a pipeline è u cunsumu d'energia aumenteranu.
Resistenza di a pipeline
A resistenza di e pipeline si riferisce à a resistenza incontrata durante u trasportu di fluidi (cum'è u fangu) in e pipeline. Sta resistenza affetta a velocità di flussu di u fluidu è a pressione. Eccu parechji fattori chjave chì affettanu a resistenza di e pipeline:
Lunghezza di a pipa: Più longa hè a pipa, più grande hè a zona di attritu trà u fluidu è a parete di a pipa, dunque a resistenza hè più grande.
Diametru di a pipa: Più grande hè u diametru di a pipa, più chjuca hè a zona relativa di cuntattu trà u fluidu è a parete di a pipa,risultante in una minore resistenza à l'attritu.
Materiali di e tubazioni: A levigatezza superficiale di e tubazioni di diversi materiali hè diversa. E tubazioni lisce producenu menu resistenza chè quelle ruvide.
Numeru di particelle in a pipeline: Più particelle ci sò in u fangu, più particelle interagiscenu è si scontranu cù u muru di a pipeline, risultendu in una resistenza aumentata.
Ostaculi in e tubazioni: cum'è i gomiti, e valvole, ecc., sti cumpunenti pruvucaranu un cambiamentu di a direzzione di u flussu di u fluidu o un aumentu di a portata lucale, aumentendu cusì l'attritu è a resistenza.
Prublemi di usura
Durante l'usu à longu andà, e pipeline di dragaggio saranu cunfruntate à diversi prublemi di usura per via di a particularità di u so ambiente di travagliu. Queste usure ponu esse principalmente divise in: usura meccanica o erosione, è corrosione chimica:
Usura meccanica o erosione: Questu hè causatu da l'attritu è l'impattu di e particelle solide (cum'è sabbia, ghiaia, fangu, ecc.) chì scorrenu in a pipeline nantu à a parete interna di a pipeline. Cù u tempu, questu effettu fisicu cuntinuu purterà à a perdita graduale di materiale nantu à a parete interna di a pipeline, in particulare in e zone cù portate più elevate cum'è i gomiti è e riduzioni di diametru, induve l'usura serà più seria.
Corrosione chimica: Durante l'usu, e pipeline di dragaggio ponu vene in cuntattu cù certi materiali corrosivi. Quessi prudutti chimichi reagiscenu chimicamente cù u materiale di a pipeline, causendu danni strutturali è degradazione di e prestazioni di u materiale di a pipeline. A corrosione chimica hè di solitu un prucessu lentu, ma quandu s'accumula per un longu periodu di tempu, pò ancu avè un impattu seriu nantu à l'integrità è a durata di vita di a pipeline.
Data: 03 di ghjugnu 2024